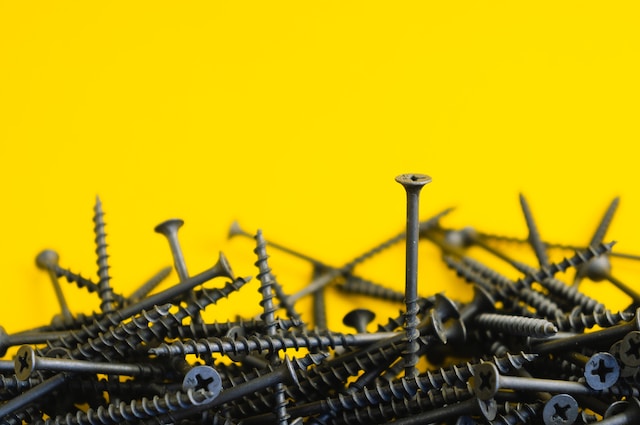
What You Need to Know About Plastic Fastener Threading
No two screws are made the same thing. Only search for all the exceptional varieties of screw heads in there. Just as there are one-of-a-kind types of screw heads that can be used with one-of-a-kind designs, the threading on such screws can also differ depending on the usefulness.
Drywall, stone, and metal all require several screw solutions, but the most complicated medium of all is plastic. Although plastic is very lightweight (which offers a wide variety of layout options), it also has a much lower content density than the others. These two properties make plastic fastening a problem.
When fastening with plastic materials, consider the screw threading.
Select a narrow flank angle
Popular type A and type AB screws are specifically designed for applications containing metal. They have a broad thread profile, known as the “flank angle,” of about 60 degrees. This induces external stress-called high radial force-and can theoretically cause damage when screwed into a softer material.
Plastic fastener threading is designed for a much narrower threading profile, which can vary from 29 degrees to 45 degrees based on the type of plastic material used. Although the same material volume as the 60-degree thread profile screws can be transferred, fasteners with a narrower thread profile can minimize radial force by half. Tri-lobed screws with slender thread angles are common in this regard because they shape deep within threads while producing less hoop tension.
With a decrease in radial stress, plastic fasteners may use smaller bolts, which can minimize the total costs of production use and molding cycle times.
Maximize stripping torque and increase pullout resistance
When it comes to plastic materials, it is also necessary to optimize the stripping torque, which is the torque required to strip the plastic thread of the fastener. Self-tap screws are typically successful in this regard, particularly if the holes are pre-drilled. The thread spacing should be larger than the traditional metal screw used.
Traditional screws can also create issues when it comes to the ability to pull-out. A wider field of thread interaction can help ensure that this doesn’t happen.
Plastic fasteners usually have a thinner, smaller diameter, and a higher thread profile, enabling the screw to hold a greater amount of material, rendering the screwless prone to drag.
Plastic-type matters
When it comes to plastic fastener threading, different types of plastics have different properties, so the type of plastic you use in your application is significant. When it comes to industrial-grade plastics, fasteners with blunt dots are safest. A fastener with a slotted shank fits well with plastics such as phenolic, although the toughest plastics can need a slotted-shank screw with a conical tip.
Any materials could also have problems with screws with plastic fastener threading. A quicker form of the nail may be the alternative because it has barbs and rings that cut into plastic more easily than regular threads.
Optimal performance / reduced cost
At the end of the day, choosing a fastener with the correct threading will guarantee maximum efficiency and decreased costs. The proper fastener will provide you with higher strip-out torque values, improved loosening resistance, and higher pull-out values. In addition to the decreased costs in terms of material utilization and processing times, you can streamline the assembly process and minimize the need for inserts and adhesives.